LUBENZ HOXX SPECIAL HYDRAULIC OIL AW 15 ISO 15 range of lubricants are supreme performance anti-wear hydraulic oils formulated with high quality base stocks and balanced additive technology. They are designed to work efficiently in hydraulic systems operating under severe conditions, where high levels of anti-wear and oil film strength protection are desired. Moreover they are also designed to work in systems where non anti-wear hydraulic oils are generally recommended.
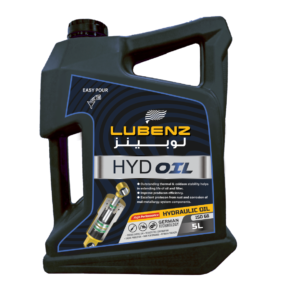
HOXX SPECIAL HYDRAULIC OIL AW 15 ISO 15
Features & Benefits
• Outstanding thermal & oxidation stability helps in extending life of oil and filter. • Superior demulsibility property of oil protects hydraulic systems from small quantities of moisture and also separates readily from larger quantities of water. • Excellent anti-wear properties and outstanding film strength provides exceptional equipment protection, that not only results in fewer breakdowns but also helps improve production efficiency. • Excellent protection from rust and corrosion of multi-metallurgy system components.
Applications
LUBENZ HOXX SPECIAL HYDRAULIC OIL AW series are suitable for use in Hydraulic systems of Industrial and Mobile equipment. • Suitable for use in Marine hydraulics, machine tools, mould injection machines and hydraulic presses. • Applications where anti-wear lubricant is required: low charged gears, bearings, air compressors etc.,
Characteristics
Specifications LUBENZ HOXX SPECIAL HYDRAULIC OIL AW series meets or exceeds following International and Builder specifications:
- DIN 51524 Part 2 HLP type
- ISO 11158 (HM fluids)
- Denison HF-0 (T6H20C)
- VICKERS M-2950S, -I-286
Typical Characteristics
LUBENZ HOXX SPECIAL HYDRAULIC OIL AW |
Test Method |
Units |
10 |
22 |
32 |
46 |
68 |
100 |
150 |
ISO Viscosity Grade |
ISO 3448 |
— |
10 |
22 |
32 |
46 |
68 |
100 |
150 |
Density @ 15 0C |
ASTM D 4052 |
gm/cc |
0.845 |
0.864 |
0.870 |
0.878 |
0.880 |
0.887 |
0.894 |
Viscosity @ 40 0C |
ASTM D 445 |
cSt |
10 |
22.9 |
32.4 |
46.8 |
68.9 |
100.8 |
150.2 |
Viscosity @ 100 0C |
ASTM D 445 |
cSt |
2.67 |
4.4 |
5.38 |
6.78 |
8.72 |
11.15 |
14.56 |
Viscosity Index |
ASTM D 2270 |
— |
102 |
100 |
98 |
98 |
98 |
95 |
95 |
Pour Point |
ASTM D 97 |
°C |
-30 |
-30 |
-27 |
-27 |
-21 |
-21 |
-18 |
Flash Point (COC) |
ASTM D 92 |
°C |
174 |
204 |
224 |
230 |
234 |
246 |
272 |
Copper Strip Corrosion |
ASTM D 130 |
— |
1B |
1B |
1B |
1B |
1B |
1B |
1B |
Rust Characteristics Proc B |
ASTM D 665 |
— |
Pass |
Pass |
Pass |
Pass |
Pass |
Pass |
Pass |
Foam Seq I,II,III |
ASTM D 892 |
ml/ml |
20/0 |
20/0 |
20/0 |
20/0 |
20/0 |
20/0 |
20/0 |
The above figures are typical of blends with normal production tolerance and do not constitute a specification.