LUBENZ ROXX SPECIAL GEARLUBE 220 ISO 220 of lubricants are supreme performance industrial gear oils, formulated with high quality base stocks fortified with sulfur-phosphorus additive system. They are designed to work efficiently in all types of enclosed gear drives with circulation or splash lubrication systems, where outstanding extreme pressure characteristics (EP/AW properties), extremely high load carrying capability and excellent demulsifying properties are desired. Moreover they offer extremely high protection against micropitting, wear and corrosion in enclosed gears and all types of oil lubricated bearings. Suitable for use in large & small spur bevel, spiral, helical & herringbone gears.
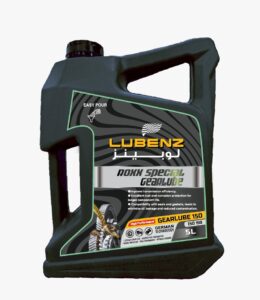
ROXX SPECIAL GEARLUBE 220 ISO 220
Features & Benefits
• High thermal & oxidation stability protects against deposit formation and oil thickening, thus enhances the life and performance of lubricant. • Excellent protection from bearing wear and high load carrying property extends the life of components. • Excellent gear protection from micropitting & scuffing and outstanding extreme pressure performance. • Excellent rust and corrosion protection for longer component life. • Compatible with elastomer seals and gaskets, leads to minimum leakage and reduced contamination. • Excellent demulsifying properties, low foaming and good air release characteristics
Characteristics
Specifications LUBENZ ROXX SPECIAL GEARLUBE series meets or exceeds following International and Builder specifications:
- DIN 51517-3 (CLP)
- ISO 6743-6 & ISO 12925-1 (CKC/CKD)
- US Steel 224
- David Brown
- Flender BA 7300, table A
- David Brown S1.53.101
Typical Characteristics
LUBENZ ROXX SPECIAL GEARLUBE |
Test Method |
Units |
46 |
68 |
100 |
150 |
220 |
320 |
460 |
680 |
AGMA 9005 |
– |
– |
– |
2 EP |
3 EP |
4 EP |
5 EP |
6 EP |
7 EP |
– |
ISO Viscosity Grade |
ISO 3448 |
– |
46 |
68 |
100 |
150 |
220 |
320 |
460 |
680 |
Density @ 15 0C |
ASTM D 4052 |
gm/cc |
0.878 |
0.880 |
0.887 |
0.894 |
0.898 |
0.900 |
0.904 |
0.910 |
Viscosity @ 40 0C |
ASTM D 4052 |
cSt |
46.8 |
68.9 |
100.8 |
150.2 |
220.5 |
320.9 |
460.8 |
680.5 |
Viscosity @ 100 0C |
ASTM D 4052 |
cSt |
6.78 |
8.72 |
11.15 |
14.56 |
18.75 |
23.95 |
30.45 |
37.85 |
Viscosity Index |
ASTM D 2270 |
– |
98 |
98 |
95 |
95 |
95 |
95 |
95 |
92 |
Pour Point |
ASTM D 97 |
°C |
-27 |
-27 |
-24 |
-24 |
-24 |
-24 |
-15 |
-12 |
Flash Point (COC) |
ASTM D 92 |
°C |
216 |
218 |
226 |
238 |
248 |
248 |
256 |
282 |
FZG Scuff Fail Stage |
A/8.3/90 |
– |
12+ |
12+ |
12+ |
12+ |
12+ |
12+ |
12+ |
12+ |
Timken OK Load |
ASTM D 2670 |
lb/kgf |
65 |
65 |
65 |
75 |
75 |
75 |
75 |
75 |
Cu Strip Corrosion |
ASTM D 130 |
– |
1B |
1B |
1B |
1B |
1B |
1B |
1B |
1B |
Rust Test-Proc B |
ASTM D 665 |
– |
Pass |
Pass |
Pass |
Pass |
Pass |
Pass |
Pass |
Pass |
Foam Seq I,II,III |
ASTM D 892 |
ml/ml |
0/0 |
0/0 |
0/0 |
0/0 |
0/0 |
0/0 |
0/0 |
0/0 |
The above figures are typical of blends with normal production tolerance and do not constitute a specification.