SPECIALTY OILS Manufacturer in Iraq
What Are Specialty Oils?
Specialty Oils are lubricants or fluids engineered to provide superior performance in specific conditions or applications. Unlike general-purpose oils, which are designed to work in a wide range of environments, specialty oils are crafted to address particular needs, challenges, or requirements.
In Iraq, specialty oils are critical due to the country’s diverse industrial activities and unique environmental conditions. The oil and gas sector, a cornerstone of Iraq’s economy, relies heavily on specialty oils for efficient operation. These oils are essential for maintaining the performance of machinery and equipment used in drilling, extraction, and refining processes. They provide vital protection against wear and corrosion, ensuring the reliability of equipment that operates under extreme conditions, such as high temperatures and pressures. Additionally, specialty oils are crucial for the agricultural sector, where they are used in machinery to enhance performance and durability, which is particularly important given Iraq’s significant agricultural activities.
Moreover, the harsh climatic conditions in Iraq necessitate the use of specialty oils with high thermal stability and resistance to oxidation. These oils help in maintaining machinery efficiency and preventing breakdowns, which is vital for sustaining industrial operations and minimizing downtime. Specialty oils also contribute to meeting regulatory standards and ensuring the safety of equipment, which is crucial for both economic and environmental reasons. In summary, specialty oils play a vital role in supporting Iraq’s industrial sectors, enhancing performance, and ensuring the longevity and reliability of machinery in challenging environments.
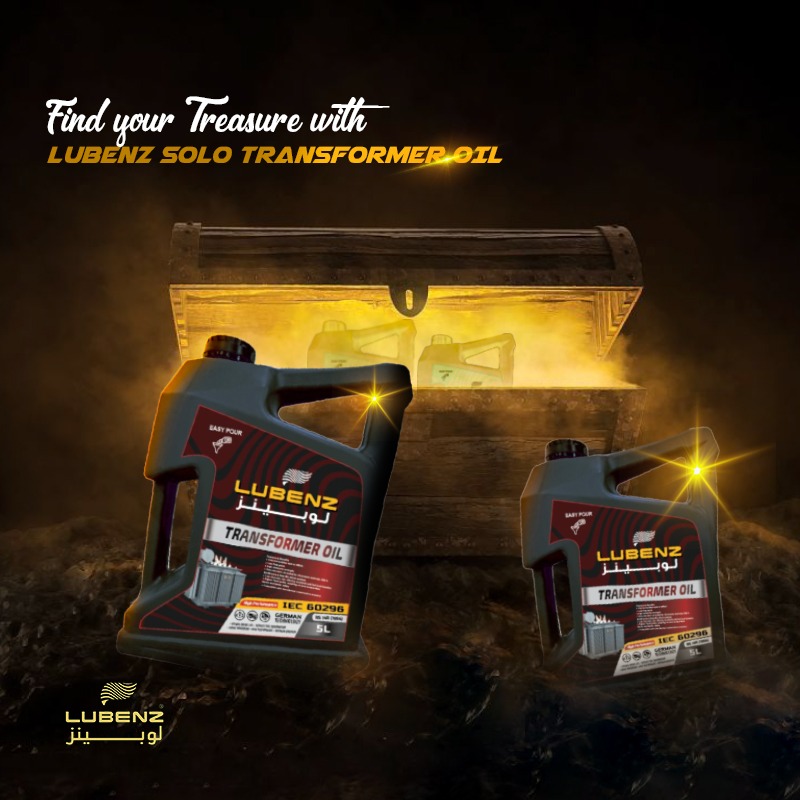
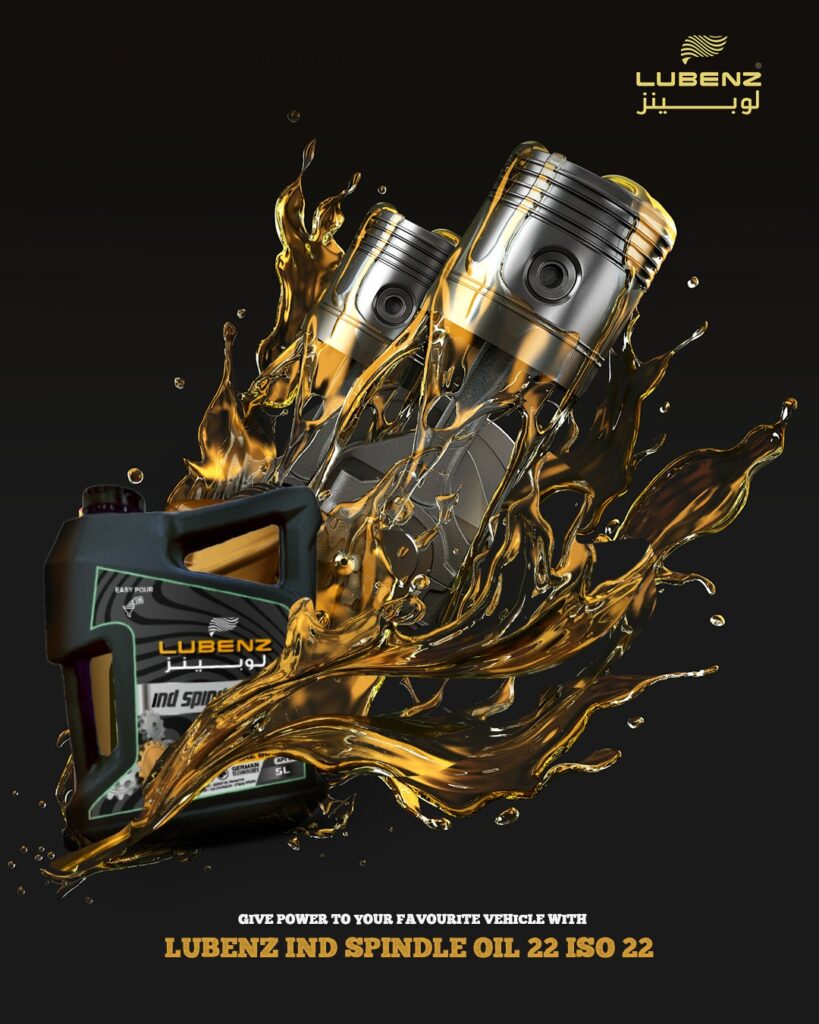
Specialty oils are designed for specific applications where standard oils may not perform adequately. They are formulated to meet unique demands in various industries. Here’s an overview of different types of specialty oils and their specific uses:
1. Hydraulic Fluids
Purpose: Hydraulic fluids are used in hydraulic systems to transmit power, lubricate components, and dissipate heat.
Characteristics: They must have a high viscosity index, good thermal stability, and resistance to oxidation. These fluids are also designed to prevent rust and foam.
Applications: Used in machinery and equipment such as excavators, forklifts, and hydraulic presses.
2. Gear Oils
Purpose: Gear oils are formulated to provide lubrication and protection for gear systems, reducing friction and wear.
Characteristics: They typically include extreme pressure (EP) additives to handle high loads and protect against gear wear and scuffing. They also need to resist oxidation and maintain stability under high temperatures.
Applications: Used in gearboxes, differential gears, and other high-load gear systems in automotive, industrial, and marine applications.
3. Turbine Oils
Purpose: Turbine oils are used in steam and gas turbines to provide lubrication, cooling, and protection.
Characteristics: They must offer excellent oxidation resistance, thermal stability, and foam control. Additionally, they should have good water separation properties and low volatility.
Applications: Employed in power generation plants, industrial turbines, and certain high-speed machinery.
4. Compressor Oils
Purpose: Compressor oils are designed to lubricate and protect compressors in refrigeration and air conditioning systems.
Characteristics: They need to handle high pressures and temperatures while providing effective lubrication and preventing carbon build-up. They also must be compatible with refrigerants and resist oxidation.
Applications: Used in air compressors, refrigeration units, and air conditioning systems.
5. Transformer Oils
Purpose: Transformer oils are used for insulation and cooling in electrical transformers.
Characteristics: They must have high dielectric strength to insulate electrical components and good thermal conductivity to dissipate heat. They should also resist oxidation and sludge formation.
Applications: Used in power transformers, electrical distribution systems, and certain high-voltage equipment.
6. Fire-Resistant Fluids
Purpose: Fire-resistant fluids are formulated to reduce the risk of fire or explosion in high-risk environments.
Characteristics: They are designed to have high flash points and contain additives that inhibit flammability. These fluids may also offer good lubrication and cooling properties.
Applications: Utilized in hydraulic systems in industries such as mining, metalworking, and aviation where fire risk is a concern.
7. Biodegradable Oils
Purpose: Biodegradable oils are designed to break down more easily in the environment, reducing environmental impact.
Characteristics: They are made from renewable resources and are formulated to degrade more quickly compared to conventional oils. They must also provide adequate performance in terms of lubrication and protection.
Applications: Used in environmentally sensitive areas such as forestry, agriculture, and marine operations.
8. Food-Grade Oils
Purpose: Food-grade oils are formulated for use in food processing and manufacturing where incidental contact with food might occur.
Characteristics: These oils meet stringent safety and hygiene standards. They must be non-toxic and free from harmful contaminants while providing effective lubrication.
Applications: Employed in food processing equipment, packaging machinery, and other equipment where food safety is a priority.
9. Specialty Engine Oils
Purpose: Specialty engine oils are designed for high-performance or racing applications.
Characteristics: They offer enhanced protection and performance under extreme conditions, such as high temperatures and high RPMs. These oils may include advanced additives to improve performance and extend engine life.
Applications: Used in high-performance vehicles, racing engines, and other demanding engine applications.
Each type of specialty oil is formulated to address specific needs and challenges, ensuring optimal performance and protection in their respective applications.
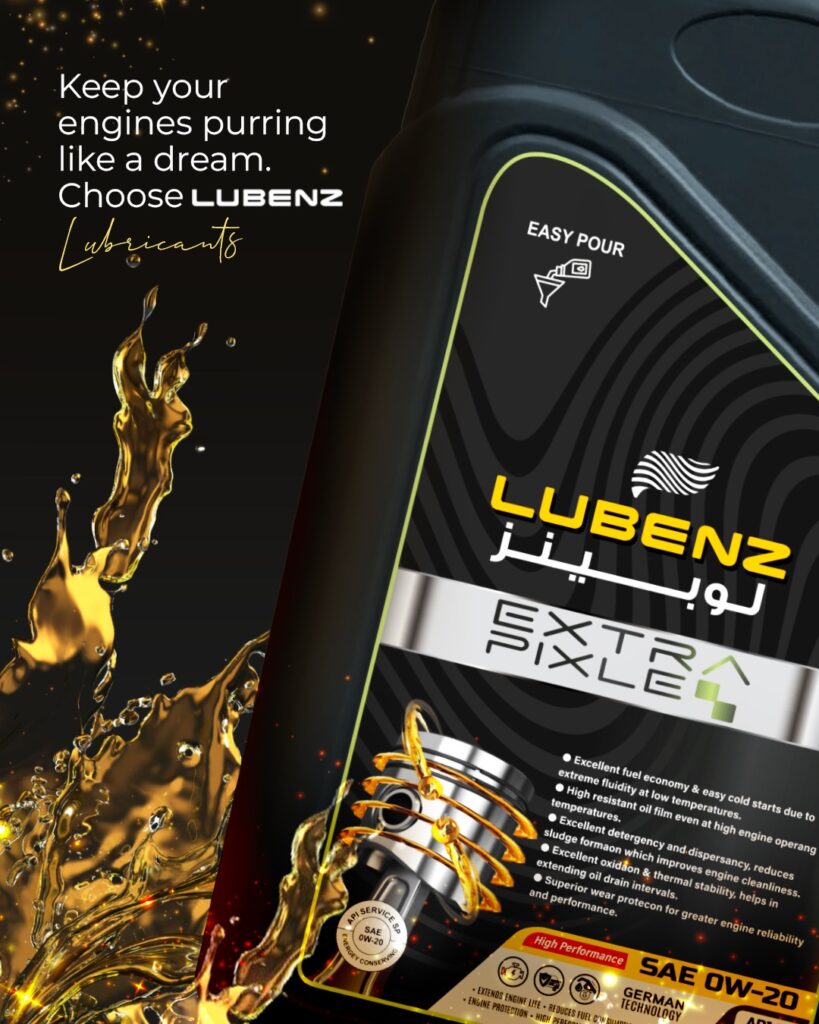